Introduction
As observed during mechanical characterization, mechanical behavior of Acrylonitrile Butadiene Styrene (ABS) specimens printed through Fused Deposition Modeling (FDM) technique is described by a linear elasticity region followed by plastic deformation. Currently there are very few studies about mechanical and strength modeling of FDM-printed materials and no one which considers material plasticity. The main goal consists in developing constitutive and strength models capable of predicting the material stiffness and strength, taking into account both linear elastic and plastic domains.
Experimental Campaign
After extracting material’s mechanical and strength properties, they are used to design optimized holed specimens (figure 1), which are subsequently FDM-printed and subjected to tensile test.
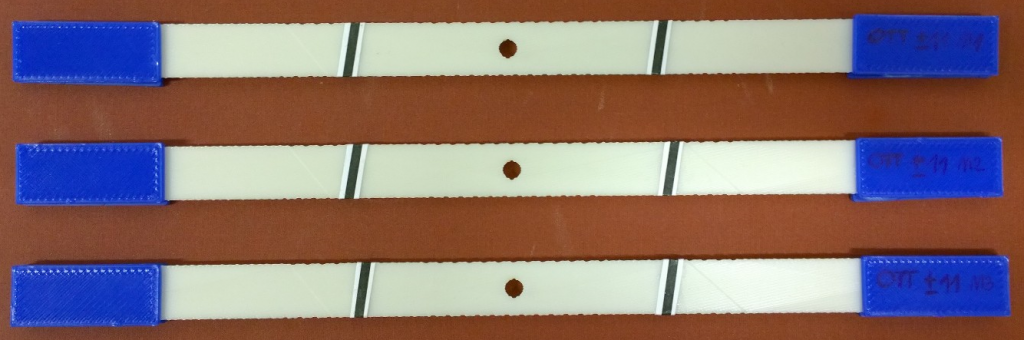
Fig. 1: FDM-printed optimized holed specimens.
First, material behavior has been described in its linear elasticity domain. FDM-printed specimens are subjected to monoaxial tensile loading. Considering Tsai-Hill yielding surface, Finite Element (FE) simulation has been found capable of predicting the material yield stress and the yielding zones, i.e. the specimen regions which start to yield.
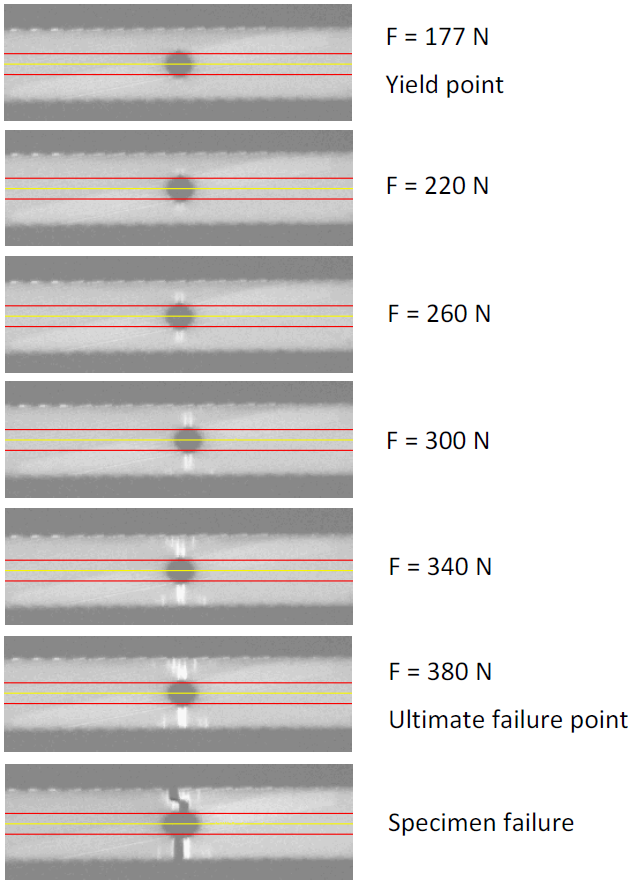
Fig. 2: Holed specimen during tensile test: yielding starts from the hole circumference and propagates perpendicularly to the loading direction.
Preliminary results show good agreement between simulation and experimental data (see figures 2 and 3). Yielding starts from the hole circumference and propagates perpendicularly to the loading direction to the specimen edges. Yielding stress value found by the FE simulation is 180 N, which is coherent with the experimental value of 177 N.
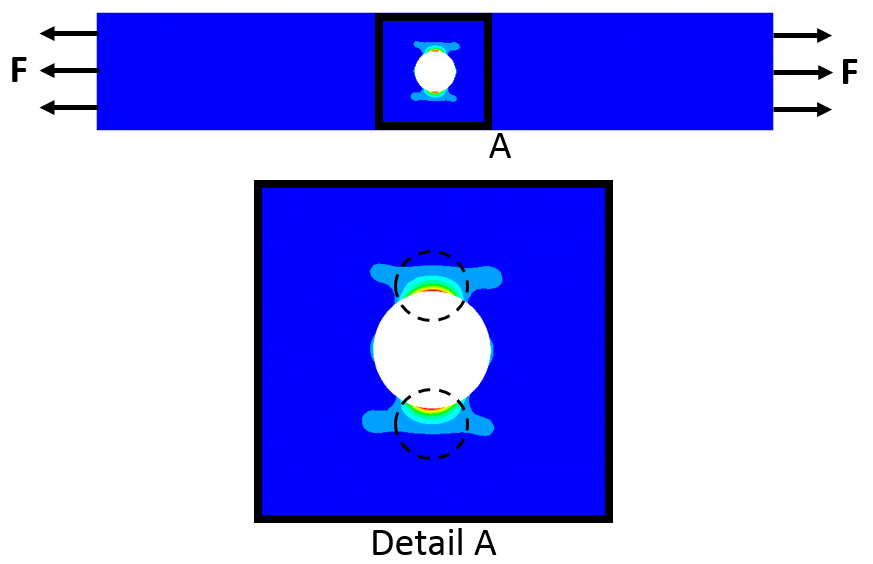
Fig. 3: Finite element simulation results: yielding starts in proximity of the hole.
To further validate the linear elastic model, different hole shapes are taken into account, e.g. ellyptic shapes (figure 4). Specimen printing, tensile tests and data elaboration have been carried out and FE simulation is in progress.
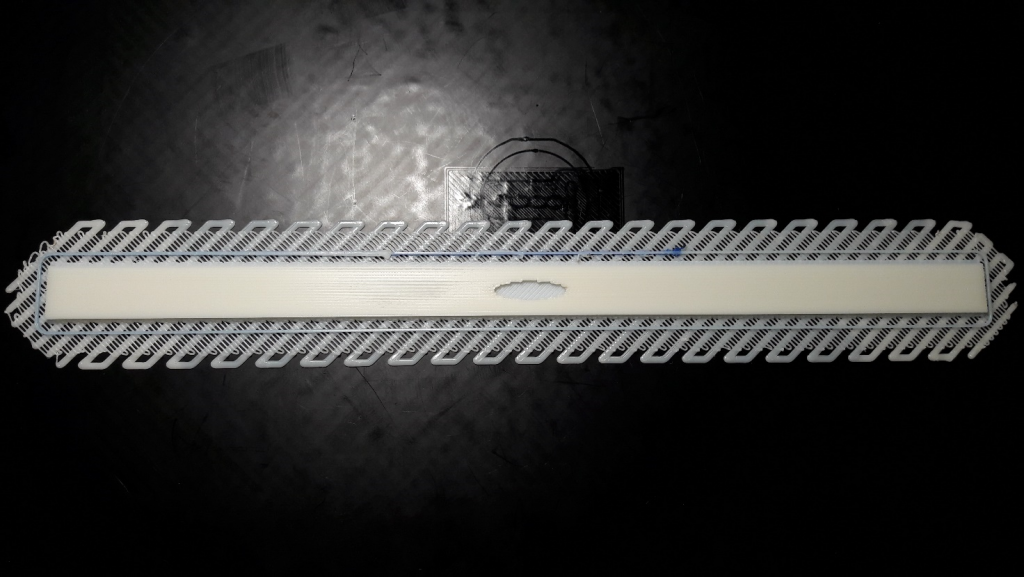
Fig. 4: FDM-printed specimens with an ellyptical hole: FE simulation is in progress.
To further describe the material behavior, plasticity must be considered, hence an elastoplastic model is under study.