Introduction
Fused Filament Fabrication (FFF) 3D-printed parts are becoming very common in industrial and consumer market-place, taking advantage from the constantly growing variety of materials that may be used, the low cost and the relatively ease of printing. FFF processes the build material by extruding a semi-molten filament through a heated nozzle in a predetermined pattern onto a heated bed, layer by layer. To a certain extent, Fused Filament Fabrication (FFF) has the potential to fabricate parts with locally controlled properties by changing printing parameters.
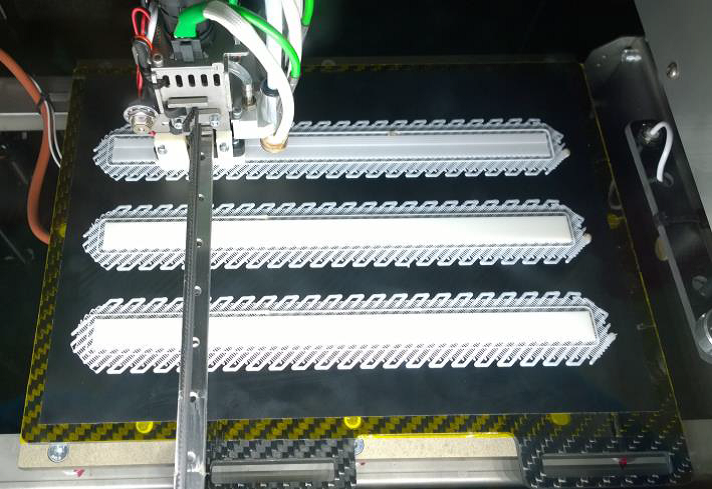
Idea
At first, a preliminary parameter assessment has been carried out, to highlight possible printing defects. Furthermore thermal distortion and support material compatibility have been tested.
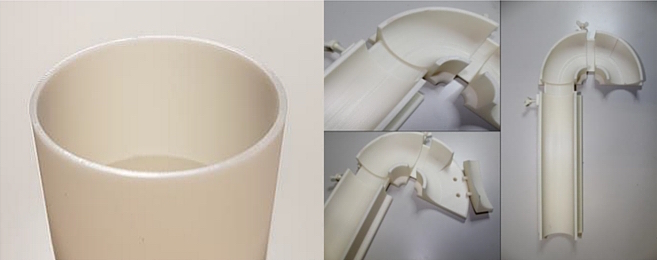
After the preliminary analysis, G-codes have been processed in order to produce suitable samples to be used in tensile tests.
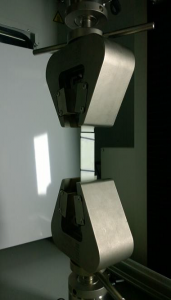
Since at the present state ad-hoc standards for specimens obtained through 3D-printing are not available, a specific standard for composite materials has been considered regarding the mechanical analysis of the material. Classical Lamination Theory (CLT) has been used to describe the mechanical behaviour of 3D-printed ABS. Moreover, Tsai-Hill failure criterion has been considered, in order to characterize the strength of the material.
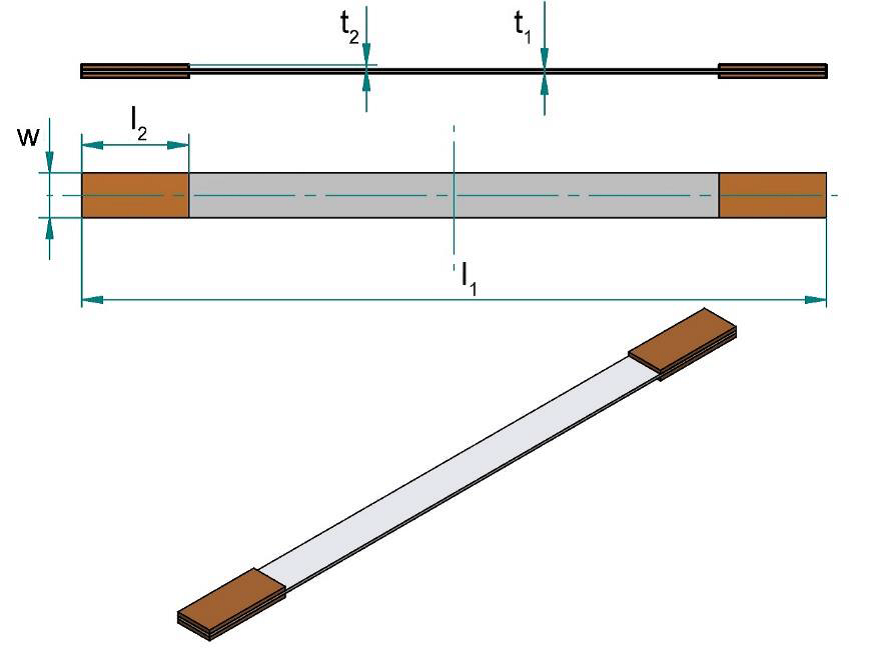
Goals
- Determine the most fitting printing parameters
- Develop a new and suitable design approach to evaluate mechanical and strength of 3D-printed materials
More than 100 samples have been tested, with a total printing time of more than 250 hours, comprehensive of initial printing trials, printing parameter assessment, failed prints and suitable samples. Preliminary results are available. The results show a good agreement with the theoretical models considered.