Introduction
Fused Deposition Modeling (FDM) 3d-printed parts are becoming very common in industrial and consumer market-place, taking advantage from the constantly growing variety of materials that may be employed, the low cost and the relatively ease of printing. Polymers such as ABS, PLA, Polycarbonate, TPU, PEEK and carbon-reinforced Nylon are successfully used in FDM processes for the production of complex-shape functional objects.
The use of such class of materials, combined with FDM technology, has becoming ever more important in structural applications thanks to some benefits such as the possibility of locally tuning mechanical properties, weight reduction, shorter time-to-market and reduced waste material. Such benefits can lead to the design of lightweight optimized components that play a crucial role in industrial applications as automotive and aerospace fields requiring less manufacturing and maintenance costs.
Idea
Traditional design methods, leveraging on computational mechanics and optimization techniques, have not yet been tailored to FDM technology to effectively support production processes and design tools.
The fabrication of well-designed and lighter products with intended density and infill at each region can be achieved using FDM processes allowing the fabrication of complex geometries without sacrificing the design requirements and constraints.
Goals
The development of new and suitable design approaches, conceived according to the specific FDM printing process are accordingly required. This goal may be achieved through the following steps:
- Experimental test: in order to evaluate mechanical properties of 3dprinted parts we are working on the definition of g-codes in order to produce suitable samples to be used in tensile tests. Moreover, there are no standard for FDM manufacturing process. Preliminary results on PLA, ABS, PC-ABS and TPU samples are now available.
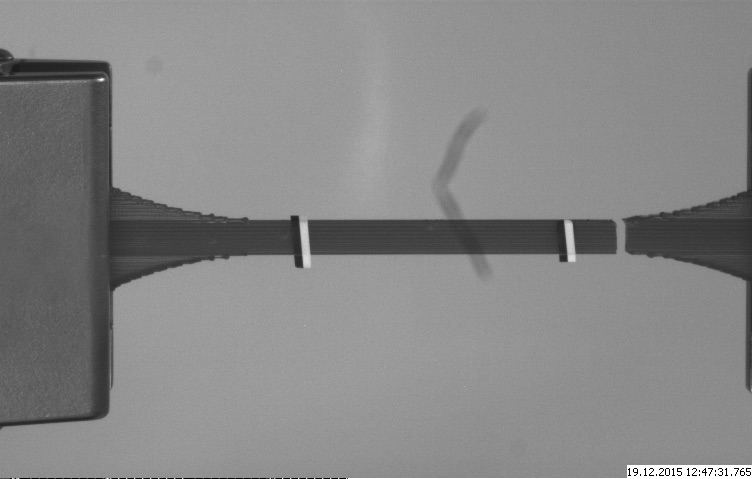
- Constitutive modelling: starting on experimental evidence, we want to employ or develop ad-hoc macroscopic constitutive models able to capture the mechanical behaviour of FDM parts.
- Optimization: current Topology Optimization (TO) techniques do not work well for FDM processes. Indeed, it is necessary to investigate i) how to apply TO to FDM parts and ii) how to convert its output to producible part by FDM technology. Moreover, for simple structural cases we have preliminary results.